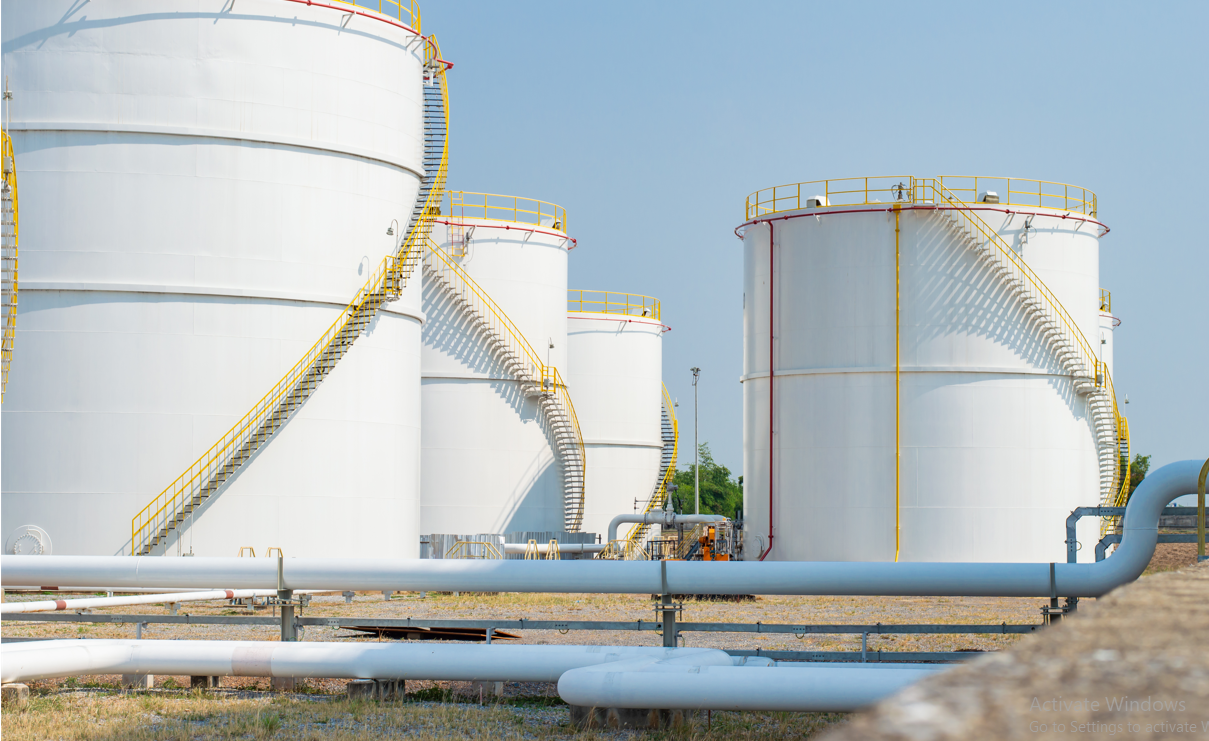
- admin
- November 17, 2021
How to Evaluate Coatings for Above Ground Storage Tanks Used in Broad Service
The application of protective industrial coatings may considerably increase the life, safety, and dependability of above ground storage tanks. Corrosion can occur when the improper coating is used or when coatings are not used at all, resulting in ruptures or even collapses that can be devastating.
The fact that many above ground storage tanks are used for extensive service to serve a wide range of ever-changing demands adds to the difficulty of choosing the correct protective tank coating. A tank used for process water, for example, may be needed to contain alkylate for 18 months. Under these new conditions, will the original coating survive, or will it require substantial restoration and re-coating costs along with downtime?
We’ll look at the impacts of corrosion on above ground storage tanks in this blog, as well as how it affects their availability and pricing over time.
Life Expectancy of Above Ground Storage Tanks
The majority of above ground storage tanks are made of carbon steel. The lifespan of a tank is estimated to be between 25 and 40 years. If no coatings are employed, corrosion on the floors and in the heat-affected zone (HAZ) areas of the tank is usually visible within 15 years of commissioning. Petrochemical compounds containing chlorides and sulfate can be extremely corrosive, resulting in rapid corrosion and potential environmental harm.
According to the American Petroleum Institute’s (API) recommendations, tanks should be inspected every three years. Many tank owners, on the other hand, strive to extend the inspection cycle for far longer periods of time, sometimes up to ten years.
Internal inspections may be extended to every five years, depending on the tank contents, if reliability-centered maintenance methods are followed. You can perhaps lengthen inspection cycles and prevent potential corrosion by choosing a coating that can survive all anticipated exposures over longer service cycles.
Taking an above ground tank out of operation is a time-consuming and expensive process. When a tank is out of operation for an extended length of time, the facility loses capacity until the tank is examined and recommissioned. When evaluating coatings as a technique of preserving tank internals against corrosion, these variables should be taken into account first.
Issues with Tank Capacity
Beyond the cost implications, re-coating tanks for new uses has a significant influence on tank farm capacity management.
There are an estimated 2,200 terminal facilities globally with a capacity of 2,750,000,000 M3 (API) of above ground storage tanks (AST).
- Based on worldwide consumption patterns, there is around 60 days of buffer capacity.
- Due to the direct impact of an out-of-service tank on supply chain balance, an increase in the total number of ASTs is necessary to maintain supply balance.
When a tank is decommissioned for inspection and repair, it is the optimum opportunity to apply protective coatings designed to withstand the widest range of exposures possible. The modest expense of applying the coating can make a big difference in reducing corrosion and metal loss, which can lead to spills. Failure to apply a coating will almost certainly lead to more expensive mechanical repairs and higher leakage hazards.
- Above Ground Storage tanks
Category
- Above Ground Fuel Tanks
- Above Ground Gas Storage Tank
- Above Ground Storage Tanks
- Above Ground Water Storage Tanks
- Agricultural Tanks
- Chemical storage Tanks
- Diesel Fuel Storage Tanks
- Diesel Storage Tanks
- Exernal FloatingRoof Tanks
- Farm Water Tank
- Fiberglass Oil Tanks
- Fiberglass Septic Tanks
- Fiberglass Tanks
- Fiberglass Underground Fuel Storage Tanks
- Field Erected Tanks
- Floating Roof Tank
- Food and Beverage Tanks
- Fuel tank
- Industrial Chemical Storage Tanks
- Industrial Gas Tanks
- Industrial Hot Water Storage Tanks
- industrial hot water tank
- Industrial Plastic Tanks
- Industrial Storage Tanks
- Industrial Tank heating pads
- industrial tanks
- Natural gas
- Natural gas vs Propane
- oil storage tank
- Oil Storage Tanks
- Peracitic Acid
- Petroleum Tanks
- Residential gasoline storage tanks
- Residential Water Storage Tanks
- Sodium Hydroxide Storage Requirements
- Sodium Hypochlorite Storage Tanks
- Steel Storage Tanks
- storage tank failure prevention
- Storage Tanks
- Sulfuric Acid Tanks
- Uncategorized
- UnderGround Storage Tanks
- Waste water tank
- Water Storage Tanks